This text was obtained via automated optical character recognition.
It has not been edited and may therefore contain several errors.
The Wallops Flight Facility, which is part of the Goddard Space Flight Center, manages and implements NASA’s sounding rocket projects which use suborbital rocket vehicles to accommodate approximately 50 scientific missions each year. These sounding rockets provide data on the Earth’s environment and also advance technology in such areas as communications and meteorology. Two facilities, a Dynamic Balance Facility and an Environmental Testing Laboratory, provide testing. The Dynamic Balance Facility at the Wallops Island facility in Virginia offers a means for dynamic and static balancing of sounding rockets, probes, and reentry and orbital vehicles to assure proper flight performance and stability. The Environmental Testing Laboratory provides for the testing of sounding rocket payloads, subassemblies and instrumentation. Other testing at the Wallops Facility involves electrical systems, attitude control and boost guidance of the sounding rockets. JET PROPULSION LABORATORY The Jet Propulsion Laboratory in California has as one of its missions the design and testing of deep space flight systems, including complete spacecraft. JPL test facilities include a 25-foot and a 10-foot space simulator with unique capabilities of precise thermal balance and design. Both simulators are capable of producing high quality space simulation for testing spacecraft under conditions of extreme cold, high vacuum and intense, highly uniform, collimated solar radiation. The JPL test facilities provide high quality empirical verification of mission performance and have supported many NASA orbital and planetary flight programs from early missions such as Mariner and Ranger to planetary spacecraft now being readied for launch. LYNDON B. JOHNSON SPACE CENTER As the focal point for America’s manned space flight program, the Johnson Space Center designs, develops and tests spacecraft and associated systems for manned space flights. Astronauts train through simulation activities covering all phases of a mission, from liftoff to landing. The center also operates the White Sands Test Facilities in Las Cruces, N.M., where propulsion systems tests are conducted. Although better known for its role in manned space flight, the Texas-based center ranks as one of the nation’s leading software production facilities. With four major software labs and thousands of employees engaged in computer work, JSC is at the heart of a software community which produces, checks and uses the complex shuttle computer codes. There are two phases of shuttle software development. The first is creation of operational increments, or versions, during which new capabilities or enhancements are added to the software code. This takes place primarily in the Software Development Facility. The second phase is reconfiguration, during which mission-unique data are applied to the base software systems to tailor them for specific flights. This phase occurs in the Software Production Facility. Validation of the software is of critical importance since every function of the orbiter is driven by computers. In the final stages of readying for a mission, the flight software undergoes integrated performance tests in the Shuttle Avionics Integration Laboratory, another of JSC’s major computer validation facilities. This lab precisely duplicates, from end-to-end, all avionics hardware as used aboard the shuttle. In addition, the software is loaded in the Shuttle Mission Simulator, the fourth principal software checkout facility. Both nominal and off-nominal runs are executed by flight crews for each mission. At the White Sands facilities, there are five operational propulsion test stands. Three of these have altitude simulation capabilities which allow propulsion systems testing to be performed in a sustained near-vacuum environment; the remaining two stands are open, or ambient, stands. JOHN F. KENNEDY SPACE CENTER The Kennedy Space Center in Florida is NASA’s primary launch center, and most ground test functions are geared toward launch operations. Both vehicles and payloads (usually complex spacecraft) must be extensively tested prior to being certified ready for flight. Spacecraft are usually fully assembled and thoroughly tested in the plant of the manufacturer before being disassembled and shipped to KSC. There are five facilities where the smaller spacecraft (or “vertically processed payloads”) are first reassembled and then thoroughly ground tested. Four of these are on Cape Canaveral and one in the industrial area of KSC. Each facility has one or two “clean rooms” which provide an ultra-clean environment. Testing usually involves some interaction with the communications and other systems which support all launches. Compatibility checks with the launch vehicle, including physical fit, electrical and mechanical connection checks and support system functions are a routine part of ground testing operations. The largest spacecraft, such as Spaqelabs and the Long Duration Exposure Facility (called “horizontally processed payloads”), are assembled and ground tested in the Operations and Checkout Building. Testing of both types of payloads can continue, on a reduced scale, right up to launch. The assembly and ground testing of Space Shuttle vehicles is the largest single responsibility of KSC. The launch itself is considered the final “test” at the end of a long series. The major shuttle components, the orbiter, solid rocket boosters and external tank, are tested and partially assembled in different facilities. Of these components, the orbiter is by far the most complex and difficult to cjround test and prepare for flight. Much of the testing is performed in the Orbiter Processing Facility, a hangar-like building designed to support orbiter assembly and test functions. Most test operations are controlled by the computerized Launch Processing System. The launch of any space vehicle is the end result of an extensive series of ground tests. This thorough testing gives a reasonable assurance that all systems will perform as expected in space.
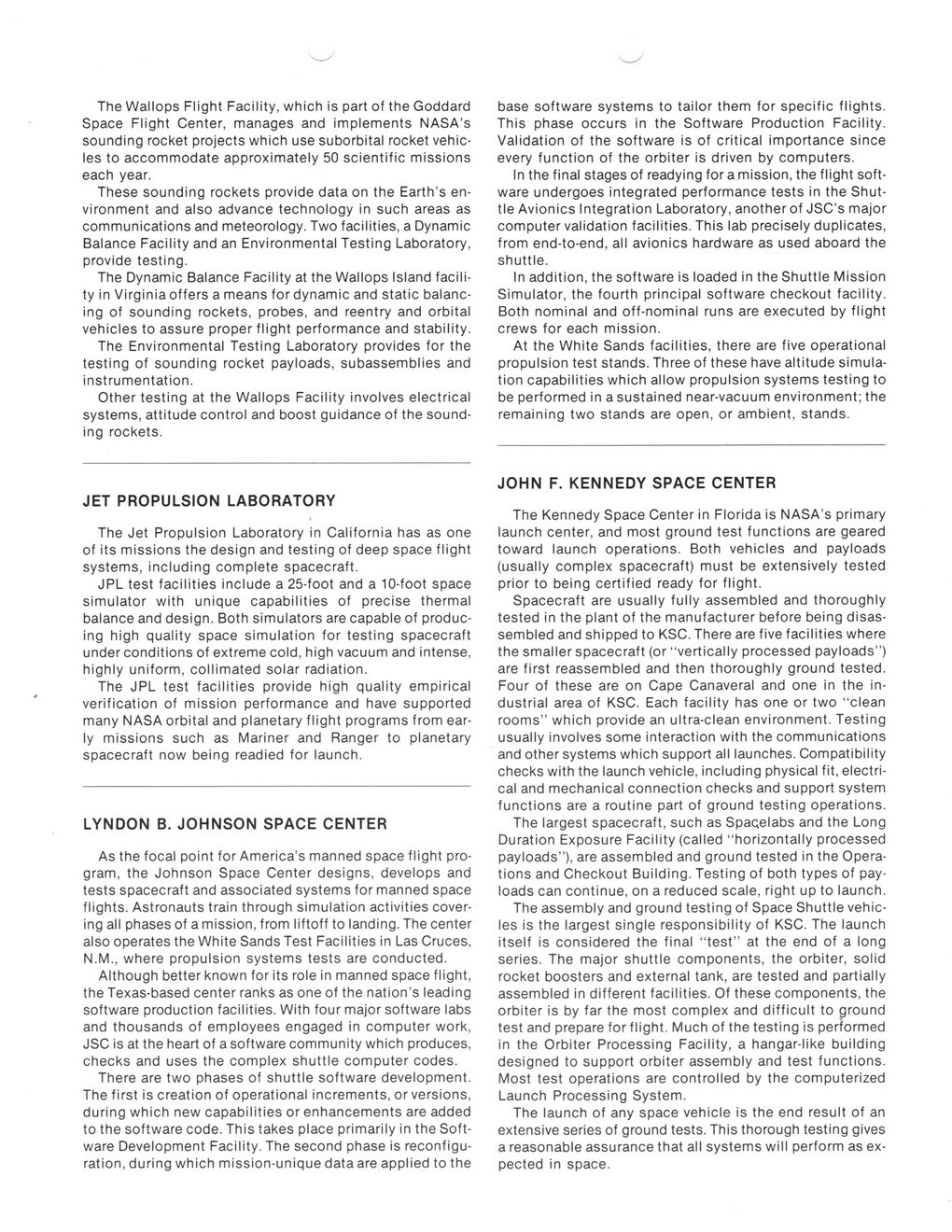
NASA Document (064)